Un nuevo edificio con capacidad para soportar el peso de las baterías de los camiones eléctricos, así como un mejor equipamiento y la reconstrucción de las plataformas logísticas, es parte de la renovación que hizo Scania de su planta de ensamblaje de chasis en Sodertalje, Suecia.
Esta remodelación, la mayor en la planta en 60 años, forma parte de la renovación de Scania para dar paso a una mayor producción de camiones eléctricos. «El año 2023 pasará a la historia de Scania como el año en que realmente ocurrió la electrificación«, señaló la marca en un comunicado.
Además de la renovación de la planta, también se desarrolló una nueva celda de batería desarrollada conjuntamente con Northvolt que durará toda la vida útil del camión; asimismo, se realizaron pruebas del sistema de carga de megavatios con ABB y el conjunto de batería junto al conjunto del chasis.
Scania afirmó que esta transición y la capacidad de aumentar la producción de camiones eléctricos es un paso vital para impulsar el cambio hacia el transporte sostenible.
«El hecho de que podamos producir camiones eléctricos combinados con motores de combustión tradicionales en nuestra fábrica es único, lo que nos hace más flexibles y rápidos a la hora de adaptar la producción a las necesidades del cliente. El personal, que es nuestro recurso más importante en esta transición, ahora está completamente capacitado en la nueva tecnología. Estamos preparados para cuando llegue el boom de los vehículos eléctricos. Por lo que veo, a medida que avanzamos juntos, nada puede detenernos», dijo Mathias Wijkstrom, Jefe de Montaje de Chasis de Scania.
Lee también: Scania entrega dos autobuses de nueva generación a ETN y Costa Line
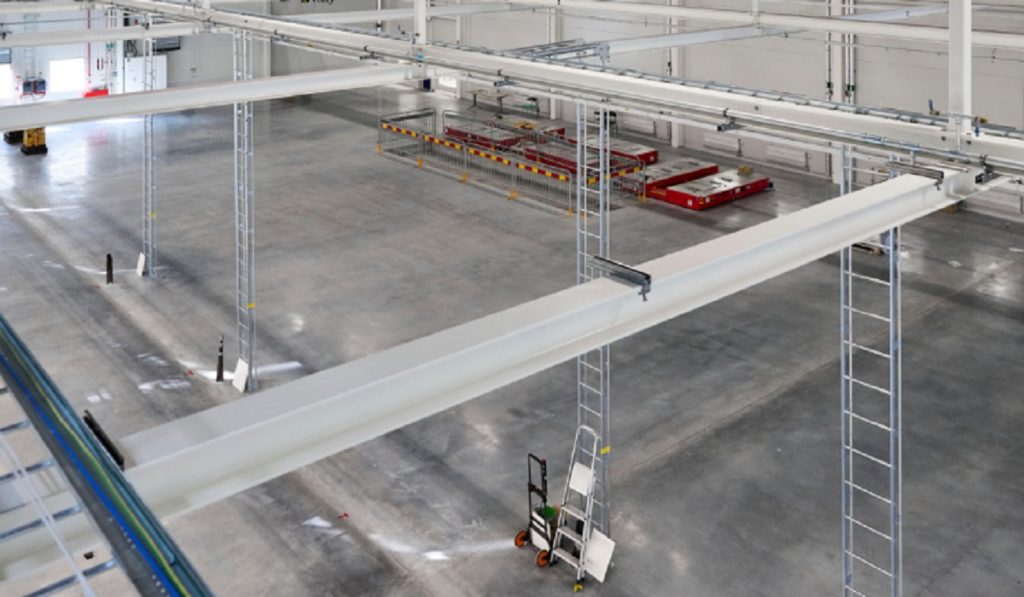
Transición industrial histórica
Scania detalló las modificaciones que tuvo la planta de ensamblaje de chasis de Sodertalje, la cual comenzó a producir camiones eléctricos en 2021; sin embargo, la fábrica tuvo que adaptarse para soportar el peso y la tecnología de los futuros camiones eléctricos.
«Estamos en medio de una transición industrial histórica y apasionante«, afirmó Wijkstrom, quien vio la fábrica cerrada durante 18 semanas desde finales de la primavera. Lo que pasó durante los meses de verano fue:
- La construcción de un nuevo edificio, equipado con equipamiento para manejar la megaestructura de baterías.
- La instalación de un nuevo sistema de línea.
- Un nuevo layout y nuevas herramientas para todas las áreas de montaje y logística.
- La reconstrucción de todas las plataformas logísticas existentes y la incorporación de una nueva.
«Las baterías añaden alrededor de cinco toneladas de peso y aumentará aún más. Nuestro suelo y nuestro equipo actuales no estaban construidos para soportar esto, por lo que necesitábamos reforzar el suelo y cambiar el sistema de líneas», advirtió el directivo
Con la remodelación, la planta ahora puede manejar tanto camiones con motor de combustión como diferentes generaciones de camiones eléctricos. Por supuesto, reunirlos todos en un solo lugar también es un desafío. «Es extremadamente difícil, tenemos un 40% más de piezas que manejar, pero el personal está preparado para llevar esta fábrica al siguiente nivel».
Te puede interesar: Ventas de Scania aumentan 19% en el tercer trimestre
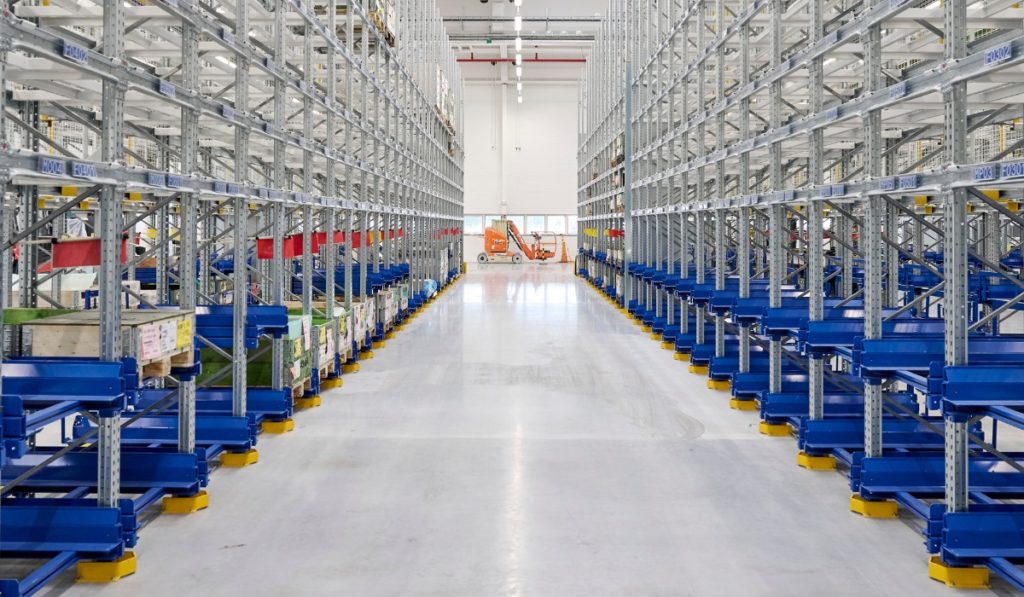
Capacitación del personal
«Y no sólo el edificio», afirma Mostafa Toweny, Director del Proyecto de Movilidad Eléctrica, «sino también las personas que trabajan allí».
El personal tuvo que capacitarse en la nueva maquinaria y procesos de la fábrica. La formación del personal se llamó «Kompetensladdningen» o «Competence Charging» y en ella participaron 200 empleados administrativos y 700 de producción, de los cuales 400 trabajan en la línea y los otros 300 en logística.
Scania trasladó unos 160 empleados a otras funciones de la empresa para reforzar esos departamentos y adquirir nuevos conocimientos. Esta capacitación se dividió en tres segmentos, cada uno de los cuales abarcó aprendizajes esenciales en lo que está por venir, o un recordatorio de los valores y conocimientos que quedan. El programa de capacitación tuvo tres fases:
- En primer lugar, se trataba de aprender sobre el producto: cómo montarlo y comprender los riesgos potenciales relacionados con los vehículos eléctricos.
- Posteriormente se trabajó en alcanzar un nivel de seguridad psicológica para trabajar con el cambio, y también para desarrollarse como equipo.
- Finalmente se elevó el conocimiento sobre el sistema de producción.
«Debería resultar seguro y emocionante trabajar con nuevos productos y que todos marquemos la diferencia en esta transición. Ha sido fácil. Todo el mundo ha puesto su corazón en esto», concluyó Toweny.
Te invitamos a escuchar el nuevo episodio de nuestro podcast Ruta TyT: