El Centro de Competencia para la Movilidad Libre de Emisiones (KEM,por sus siglas en alemán: Kompetenzcenter für emissionsfreie Mobilität) está celebrando 30 años de operaciones, tiempo en el cual se ha convertido en punta de lanza de la compañía en el desarrollo y producción de componentes y vehículos con propulsión alternativa.
En el KEM, Daimler Truck construye prototipos, produce series pequeñas y prepara la puesta en marcha de series. De este modo se cierra la brecha entre el desarrollo de componentes y vehículos electrónicos y la producción a gran escala.
Fundado en 1994, el KEM fue al principio un taller solamente experimental para nuevas propulsiones. Uno de los primeros proyectos de 1996 fue la producción de vanes eléctricas.
En vista de la creciente relevancia de las propulsiones alternativas en los últimos años, Robert Braun, Director del Centro de Competencia para la Movilidad Libre de Emisiones, destacó: «Durante los últimos 30 años hemos adquirido mucha experiencia con diversas tecnologías y, con los conocimientos adquiridos gracias a ello estamos perfectamente posicionados para el futuro. Podemos decir con orgullo que hay una parte de la experiencia de KEM en cada vehículo con propulsión alternativa de Daimler Truck».
Actualmente, la atención del KEM se centra en la integración y transferencia a la producción en serie de propulsores alternativos eléctricos y basados en hidrógeno. La concepción de líneas de producción con las últimas tecnologías de cero emisiones es una de las principales competencias de KEM.
Con amplios conocimientos técnicos, más de 50 ingenieros, maestros artesanos e ingenieros mecatrónicos definen en el KEM nuevos procesos de fabricación para componentes de vehículos con o sin emisiones, como paquetes de baterías, sistemas de baterías o unidades de pila de combustible y depósitos de hidrógeno.
Lee también: Accelera, Daimler Truck y PACCAR finalizan la creación de Amplify Cell Technologies
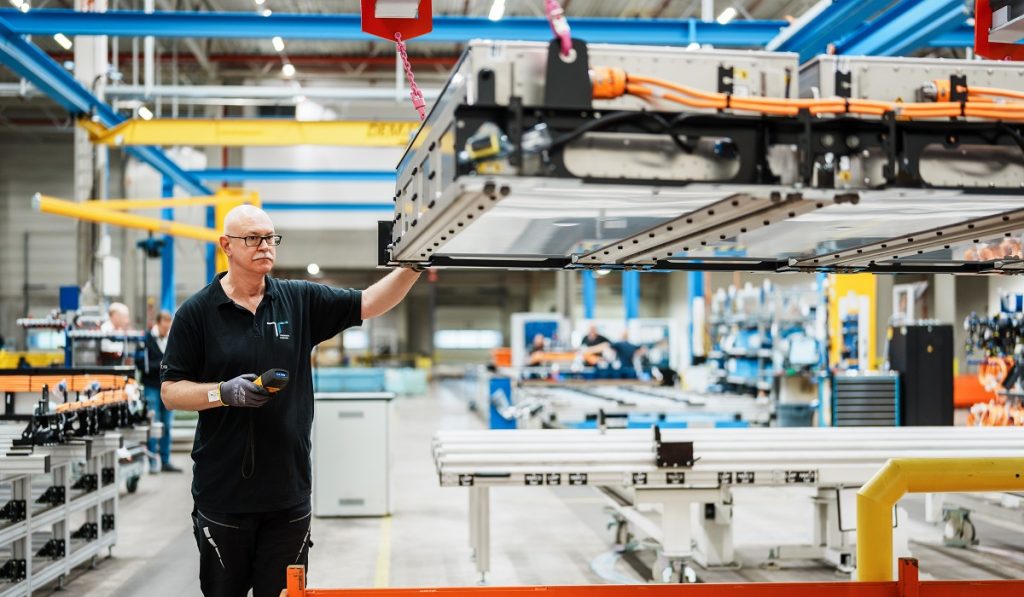
Baterías para el eCitaro
Daimler Truck explicó que el KEM ya participó en el aumento de la producción en serie del autobús urbano totalmente eléctrico Mercedes-Benz eCitaro, que se fabrica en Mannheim desde finales de 2018. Desde entonces, en KEM se ensamblan y prueban paquetes de baterías para formar los llamados clusters de baterías de alto voltaje.
Esto también está previsto para la próxima generación de baterías de autobuses eléctricos, que se utilizarán a partir de mediados de la década. A continuación, los sistemas de baterías se instalan en el techo durante el montaje del autobús.
Es de destacar que todos los vehículos de pila de combustible Mercedes-Benz eCitaro llegan a KEM una vez finalizados para la recarga inicial en la propia estación de hidrógeno del centro.
Andreas Moch, Jefe de Obra de la Planta de Mercedes-Benz en Mannheim, comentó: «Ampliamos continuamente nuestro papel en el camino hacia un transporte neutro en emisiones de CO2 en Sede de Mannheim. El año que viene queremos abrir nuestro Battery Technology Center, donde, entre otras cosas, crearemos nuestra propia línea piloto para la producción de prototipos de celdas de batería. Al mismo tiempo, nos preparamos para el inicio de la producción en serie de la llamada caja frontal, un módulo importante para el eActros 600».
Te puede interesar: Daimler Truck México y distribuidores arrancan la recertificación Evolución Elite

Baterías para el eActros
De la misma manera, el KEM está presente en el eActros 300/400 y eEconic de la planta de Mercedes-Benz en Mannheim. Para los camiones eléctricos que se fabrican actualmente en la planta de Mercedes-Benz en Wörth, a unos 50 kilómetros de distancia, se instalan módulos de batería individuales en el KEM para formar un sistema completo de baterías.
Pero antes de convertir los módulos en una batería de alto voltaje lista para usar, el primer paso es colocar los módulos individuales en una carcasa de batería. Luego conectarlos a otros componentes como barras colectoras, dispositivos de control y cables. A continuación se cablean los juegos de cables de alta tensión y se aplican capas de aislamiento para garantizar los más altos estándares de seguridad.
Finalmente, en la carcasa metálica premontada se fija la denominada caja eléctrica/electrónica (E/E box), que posteriormente constituye la interfaz entre la batería y el vehículo. La caja E/E también está premontada en el KEM. Después de una última prueba funcional y de estanqueidad de toda la batería de alto voltaje, se envía a Wörth.
Te invitamos a escuchar el nuevo episodio de nuestro podcast Ruta TyT: